G.17.4.2.1.9 Hinge Formation and Hinge Unloading
This section describes how the program handles the formation of hinges and the resulting redistribution of load.
Moment Diagrams With Hinges
For each load increment, member sectional forces are checked with section capacity in order to check formation of hinge. If sectional force exceeds section capacity, hinge formation starts. This implies member lies on or beyond point B on the load deformation curve. The point B in the load deformation curve denotes the yield point of the hinge. The hinge is assumed to be rigid between points A and B until it yields.
When the hinge reaches the deformation denoted by point C, it begins to lose load carrying capacity. When it reaches the deformation point E, the hinge loses all of its load carrying capacity.
Total numbers of 13 sections along the length of member are scanned for Mz and My moments. Maximum moment is located and checked with section capacity. If the sectional force exceeds section capacity the material starts yielding at that particular location and the hinge at this particular position lies on point B on load deformation curve.
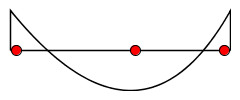
Typical beam moment diagram under gravity load, with super-imposed hinges
If bending moment diagram is like figure 1.8 (this happens at initial stage of load increment when push load is much low as compared to dead load) the chance of forming moment hinge is at two ends and at span of the member (as shown by red dots).

Typical beam moment diagram under significant lateral load, with super-imposed hinges
If bending moment diagram is like figure 1.9 (this happens when push load is much high as compared to dead load) the chance of forming moment hinge is only at sections at or nearer to two ends of the member (as shown by red dots).
Method of Hinge Unloading
When a hinge unloads, the program must find a way to remove the load that the hinge was carrying and redistribute it to the rest of the structure. Hinge unloading occurs whenever force-deformation or moment-rotation curve shows a drop in capacity, from point C to point D. The hinge unloads elastically without any plastic deformation (i.e., parallel to slope A-B).
When the hinge force reaches point C, entire structure is unloaded i.e. the program reverses the load on the whole structure until the hinge is unloaded up to the point D. When the hinge reaches point D, the load is again reversed. Other parts may now pick up the load that was removed from the unloading hinge.