Introduction to Parametric Modeling
Parametric modeling tools give you a degree of flexibility which is not possible with conventional 3D tools. Parametric modeling allows complex elements to be edited easily without the need to be manually rebuilt. For example, the parameters used to create an object may be changed afterward to achieve a different result without manually rebuilding the element. Modifications to elements can be made by selecting and using handles to make changes interactively, or by changing the object's parameters in the element's Properties dialog.
- Create a 2D parametric sketch (profile)
- Apply constraints to the 2D parametric profile
- Create a 3D parametric element using the 2D profile
- Modify the 3D element using handles or changing the parameters
- Apply constraints to the 3D parametric elements
- Apply variable-driven features to create complex design components
- Reuse the complete component by placing it in another design as parametric Cell
Parametric elements keep a record of how objects are built. When you change parameters in the element, the element is updated automatically. MicroStation re-executes the operations used to create the object using the new inputs to generate a new result.
- Design alternatives - Try and test various sizes or parameters to determine which is the best by simply adjusting the model parameters getting a new result every time.
- Accommodating changes - Save time by editing a part without having to recreate it.
- Managing complexity - Create intricate, variable-driven parts with relationships that would be too complex to maintain manually.
In parametric modeling, designs are driven by their inputs - property values, profiles, and operand objects used to create them - the inputs stay connected to the outputs. It is not necessary to get the perfect result on the first try, but it is easy to change specific values later. An object needs only to be the approximate size and shape of the intended element being created, as dimensions can be adjusted or constraints can be added later to change the shape of the geometry to get the desired shape.
For example, when you move a parametric entity, such as a hole, to another location on a solid, the hole correctly re-orients itself relative to the solid it cuts. On completion of the move the solid regenerates automatically to reflect the change.
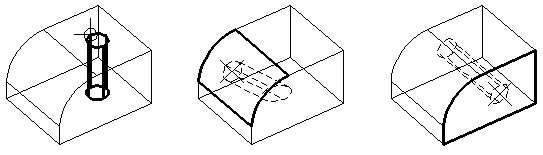